Discover how Decoiling Straightener Cutter Machines revolutionize rebar processing by ensuring precision, efficiency, and cost-effectiveness. Learn their role in modern construction and manufacturing.
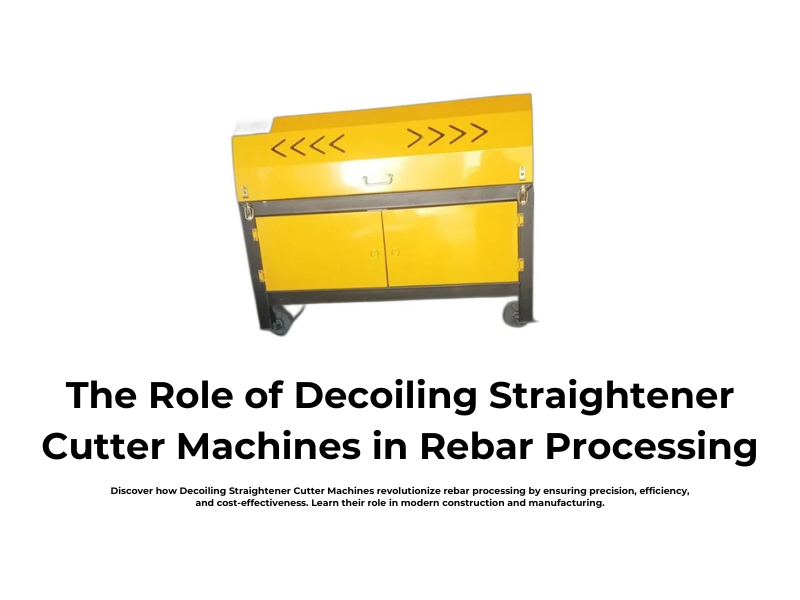
Reinforcing bars (rebars) are critical to the structural integrity of buildings and infrastructure projects. To ensure their effectiveness, precision and consistency in their production and processing are paramount. Among the various machinery that play a pivotal role in rebar processing, Decoiling Straightener Cutter Machines stand out as indispensable tools. These machines streamline operations, reduce manual labor, and enhance the overall quality of the output, making them vital in construction and manufacturing industries.
In this article, we delve into the critical role Decoiling Straightener Cutter Machines play in rebar processing. We’ll explore their working principles, advantages, and applications, shedding light on why they have become a cornerstone of modern rebar production.
Understanding Decoiling Straightener Cutter Machines
What Are Decoiling Straightener Cutter Machines?
Decoiling Straightener Cutter Machines are advanced industrial machines designed to process rebars by decoiling them from coils, straightening the bars, and cutting them to desired lengths. These machines are integral to rebar manufacturing facilities, as they help achieve precision and consistency while reducing material waste.
The machine combines three primary functions:
- Decoiling: Unwinding rebars from large coils.
- Straightening: Correcting bends and irregularities to ensure uniformity.
- Cutting: Segmenting rebars into required lengths based on project specifications.
Key Components of the Machine
- Decoiler: Holds the rebar coil and feeds it into the straightening mechanism.
- Straightening Unit: Utilizes rollers or mechanical guides to straighten the rebar.
- Cutting Mechanism: Features blades or shears to cut the rebar accurately.
- Control Panel: Allows operators to configure and monitor operations.
- Safety Features: Includes emergency stop buttons, protective guards, and automated shutoff mechanisms.
The Importance of Decoiling Straightener Cutter Machines in Rebar Processing
1. Enhanced Efficiency
Manually decoiling and straightening rebars is time-consuming and labor-intensive. Decoiling Straightener Cutter Machines automate these processes, drastically reducing the time required for preparation and increasing overall productivity.
2. Precision and Consistency
Construction projects demand rebars of precise lengths and uniform straightness. These machines ensure that every bar meets stringent quality standards, minimizing discrepancies and enhancing structural reliability.
3. Reduction in Material Waste
Manual processing often leads to significant material wastage due to errors. Automated machines optimize material usage by ensuring precise cuts and reducing offcuts, contributing to cost savings.
4. Improved Workplace Safety
Rebar processing can be hazardous when done manually. Decoiling Straightener Cutter Machines come equipped with safety features that protect operators and reduce the risk of accidents.
5. Cost-Effectiveness
Although the initial investment in these machines may be substantial, the long-term savings on labor, material, and time make them a cost-effective choice for rebar processing.
Working Principles of Decoiling Straightener Cutter Machines
1. Loading the Rebar Coil
The process begins with loading a rebar coil onto the decoiler. This component unwinds the coil and feeds it into the straightening unit. Advanced machines allow for automated coil loading, further reducing manual intervention.
2. Straightening
As the rebar passes through the straightening unit, a series of rollers or guides corrects bends and irregularities. This ensures the rebar’s uniformity, which is essential for structural integrity.
3. Measuring and Cutting
The machine is pre-programmed to cut rebars into specific lengths. Sensors measure the length as the rebar advances, and the cutting mechanism activates at the appropriate moment to ensure accuracy.
4. Output and Collection
The processed rebars are collected in a designated area, ready for further use or transportation to construction sites.
Applications of Decoiling Straightener Cutter Machines
- Construction Industry
- Preparing rebars for residential, commercial, and industrial buildings.
- Ensuring precision in high-rise structures and bridges.
- Infrastructure Projects
- Processing rebars for roads, railways, and dams.
- Supporting the production of precast concrete components.
- Manufacturing
- Fabricating metal frameworks and machinery parts.
- Creating custom rebar configurations for specific applications.
- Automotive Sector
- Producing metal rods for vehicle frames and suspension systems.
- Streamlining the manufacturing of industrial-grade springs.
Advantages of Using Decoiling Straightener Cutter Machines
1. Automation and Precision
These machines operate with minimal human intervention, ensuring precision and repeatability in rebar processing.
2. Flexibility
Modern machines can process rebars of various diameters and lengths, accommodating diverse project requirements.
3. Durability and Longevity
Constructed from robust materials, these machines are designed to withstand heavy-duty operations, ensuring a long service life.
4. Eco-Friendly Operation
By minimizing waste and optimizing energy consumption, these machines contribute to sustainable manufacturing practices.
5. Ease of Maintenance
Many machines are designed with modular components, allowing for easy maintenance and reducing downtime.
Challenges and Considerations
While Decoiling Straightener Cutter Machines offer numerous benefits, they also present certain challenges:
- Initial Investment The upfront cost of purchasing and installing these machines can be high, which may be a barrier for small-scale operations.
- Skill Requirements Operators need proper training to configure and maintain the machines effectively, adding to operational costs.
- Space Requirements These machines require a significant amount of floor space, which may be a constraint for smaller facilities.
- Energy Consumption High-powered machines can increase energy bills, necessitating efficient energy management.
Future Trends in Decoiling Straightener Cutter Machines
The field of rebar processing is continuously evolving, with innovations aimed at enhancing efficiency and sustainability. Key trends include:
- Integration of AI and IoT Advanced machines are incorporating artificial intelligence (AI) and the Internet of Things (IoT) to optimize operations and provide real-time monitoring.
- Green Manufacturing Practices Eco-friendly designs, such as energy-efficient motors and recyclable components, are becoming standard.
- Compact Designs Manufacturers are developing compact machines to cater to facilities with limited space.
- Enhanced Safety Features Future machines are likely to feature more sophisticated safety mechanisms, such as automatic hazard detection and AI-based safety protocols.
Conclusion
Decoiling Straightener Cutter Machines have revolutionized the rebar processing industry by combining efficiency, precision, and safety. Their ability to automate complex processes while maintaining high standards of quality makes them indispensable in modern construction and manufacturing.
As technology continues to advance, these machines will play an even more significant role in shaping the future of rebar processing. Investing in Decoiling Straightener Cutter Machines is not just a step toward operational excellence but also a commitment to sustainable and innovative practices in the construction industry.